L’entreprise LAPP est un fournisseur leader en solutions intégrées et de produits de marque dans le domaine du câble et des connexions au niveau mondial. Fondée en Allemagne en 1959, LAPP est désormais présente dans plus de 80 pays avec environ 5700 employés et 26 sites de production. En France, le site de production de Forbach s’est spécialisé dans la production de câbles souples, essentiellement pour l’industrie.
Le site de Forbach comprend 2600 références produits, avec l’arrivée récente de câbles de recharge pour voitures électriques et panneaux photovoltaïques. Ces nouvelles références demandent aux équipes d’apprendre continuellement de nouvelles méthodes, mais aussi de transmettre ces compétences clés aux nouveaux arrivants. Avec environ 280 collaborateurs en incluant les intérimaires, la formation est primordiale à Forbach pour standardiser les procédures et assurer la polyvalence des équipes.
Julien Mazelin, Directeur Général des Câbleries LAPP à Forbach, confirme l’importance de la formation et la transmission des savoir-faire chez LAPP : « Notre métier est très technique et ne peut être automatisé à 100%. Il est important que nos collaborateurs soient formés dès le départ aux bons gestes et bonnes pratiques. C’est ce qui nous permet de toujours assurer la qualité de nos produits, faisant la renommée de LAPP aujourd’hui. ».
En effet, les formations peuvent être longues chez LAPP, représentant en moyenne sept semaines pour qu’un technicien devienne autonome. La mobilisation des experts qualifiés pour assurer le compagnonnage des nouveaux techniciens représente également une charge importante. Les équipes recherchent donc une solution permettant de réduire drastiquement les temps et coûts de formation, tout en permettant une montée en compétences plus autonome. C’est dans cette optique que la solution Dimeo fut choisie.
Le déploiement de la solution Dimeo chez LAPP
Les échanges avec LAPP commencent en Juillet 2024, suite à la mise en relation par une entreprise déjà équipée de la solution Dimeo. Ces échanges ont permis de découvrir Dimeo à travers une courte démonstration, mais également les possibilités qu’apportent la réalité mixte et l’intelligence artificielle au sein du milieu industriel. Les équipes confirment leur volonté de tester la solution lors d’un Proof of Concept (POC) sur site pour l’appliquer à leurs cas d’usage.
Deux journées d’accompagnement sont ensuite organisées en Octobre 2024. L’objectif pour LAPP est de confirmer la rapidité et simplicité d’usage de la solution pour digitaliser ses procédures métiers en tutoriels intuitifs. Le service méthodes a ainsi pu visualiser et comprendre comment créer les modules de A à Z. Ces modules étaient ensuite mis à disposition des experts métiers et des apprenants afin d’observer et tester les procédures intuitives finalisées. Les retours d’expérience furent largement positifs, permettant au site de Forbach de passer à l’étape suivante.
LAPP effectue ensuite un essai de la solution sur 2 mois. L’essai comprend la location d’un casque de Réalité Mixte ainsi que l’accès à Dimeo. L’objectif est de valider l’autonomie à l’usage, mais également confirmer l’ensemble des cas d’usage applicables. Jonathan Verderame, Superviseur des opérations des Câbleries LAPP à Forbach, nous raconte : « L’essai nous a permis d’appliquer le logiciel à de nombreux cas d’usage. Ce qui nous a confortés dans notre choix, c’est le module de changement d’outillage que nous avons réalisé en interne. Une stagiaire qui n’avait jamais réalisé l’opération s’en est très bien sortie en autonomie grâce au logiciel, c’est un véritable outil pédagogique. »
En Décembre 2024, LAPP démarre officiellement ses usages internes avec 3 casques de Réalité Mixte répartis au sein de l’usine de Forbach. Une formation est effectuée sur site avec Innoteo pour accompagner le service méthodes dans la conception des 1ers modules. Les équipes poursuivent désormais la conception et la diffusion des modules en autonomie, afin de répondre aux besoins et objectifs fixés.
Une stagiaire qui n’avait jamais réalisé l’opération s’en est très bien sortie en autonomie grâce au logiciel, c’est un véritable outil pédagogique.
Jonathan Verderame – Superviseur des opérations des Câbleries LAPP à Forbach
Les besoins et objectifs identifiés par LAPP
Suite aux premières discussions, les équipes ont identifié plusieurs sujets auxquels la solution devait répondre afin de justifier son déploiement. L’objectif principal était de permettre aux équipes de répondre à ces enjeux par eux-mêmes, grâce à la maîtrise du logiciel en autonomie.
- Optimiser la formation des nouveaux opérateurs dès leur arrivée.
- Améliorer l’efficacité des opérateurs déjà en place en maintenance.
- Standardiser les procédures en appliquant les bonnes pratiques.
- Faciliter le rafraichissement des gammes de contrôles.
L’entreprise a choisi de déployer la solution progressivement. L’objectif est de cibler en premier lieu les opérations où la valeur ajoutée est la plus forte. Les experts métiers sont ainsi incités à utiliser le casque et Dimeo, pour faciliter les opérations pouvant s’avérer complexes. Cette méthode permet de ne pas forcer l’usage. Elle permet également de démocratiser progressivement le casque dans les habitudes et discussions d’entreprise. LAPP constate ainsi un usage progressif et volontaire de ses équipes. L’accueil de cette innovation est perçu comme un gain de confort et de temps lors des opérations.
Habituellement, les techniciens travaillent avec des procédures au format PDF ou papier. Ce format standard présente des avantages, mais aussi plusieurs limites pour LAPP. Les apprenants peuvent avoir du mal à se représenter les gestes techniques précis à effectuer, et peuvent se retrouver perdus pour situer les actions dans l’atelier. LAPP peut désormais proposer une alternative plus intuitive avec les modules Dimeo. Ces modules contiennent des visuels interactifs et multimédias, tels que des vidéos et des indications visuelles grâce à la Réalité Mixte.
La Réalité Mixte pour faciliter les formations
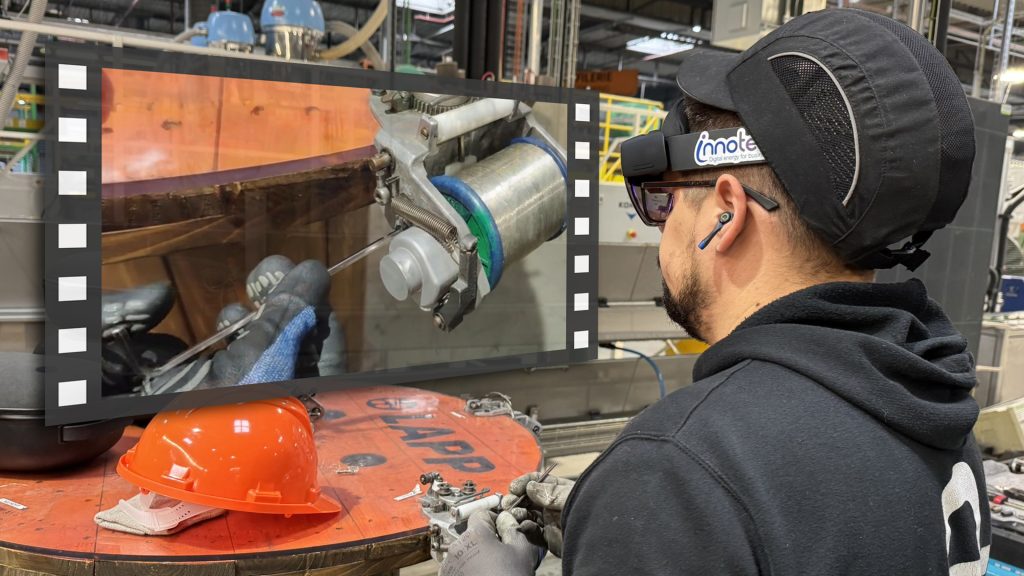
La Réalité Mixte permet d’ajouter des aides visuelles au sein de l’atelier. Ces aides sont positionnées afin d’illustrer un chemin à emprunter, un bouton sur lequel appuyer, ou une machine à utiliser. Elles permettent notamment de situer l’action demandée en un seul coup d’œil. Les casques de Réalité Mixte proposent ainsi le visionnage de ces informations directement en atelier. L’apprentissage se réalise ainsi par la pratique et de manière visuelle, avec un contenu interactif.
Le premier module réalisé est une présentation de ligne avec des indications 3D. Ces indications mettent en surbrillance les composants et leurs mouvements, afin d’illustrer le fonctionnement de la ligne, même à l’arrêt. L’intégration de vidéos explicatives tournées en interne ou trouvées sur internet permet de montrer comment y sont fabriquées les pièces. Ce module est à destination des nouveaux arrivants, des visiteurs, mais également des opérateurs qui ne connaissent pas l’ensemble de la chaîne.
Ce guidage augmenté permet également de réduire les erreurs. L’exemple concret est le changement d’articles, pouvant différer d’un produit à un autre, mais aussi d’une machine à une autre. Pour faciliter ces changements, les équipes ont intégré des questions au sein des modules. Ces questions permettent d’adapter automatiquement le parcours et les aides visuelles aux réponses données. Par exemple, les emplacements où aller chercher le produit, ranger l’ancien et positionner le nouveau, changent selon les produits et la machine renseignés par l’utilisateur lors de son parcours. Une flèche en surbrillance guide toujours visuellement le technicien au bon endroit.
Les nouveaux arrivants apprennent plus vite chaque opération, avec la possibilité de s’entraîner et rejouer chaque scénario en totale autonomie. L’accès aux formations est également facilité avec des casques mis à disposition à cet effet, avec une multitude de modules disponibles. Le service méthodes a déjà listé les procédures prioritaires et poursuit actuellement leur digitalisation grâce aux outils d’intelligence artificielle intégrés à Dimeo.
Une conception assistée par l’intelligence artificielle
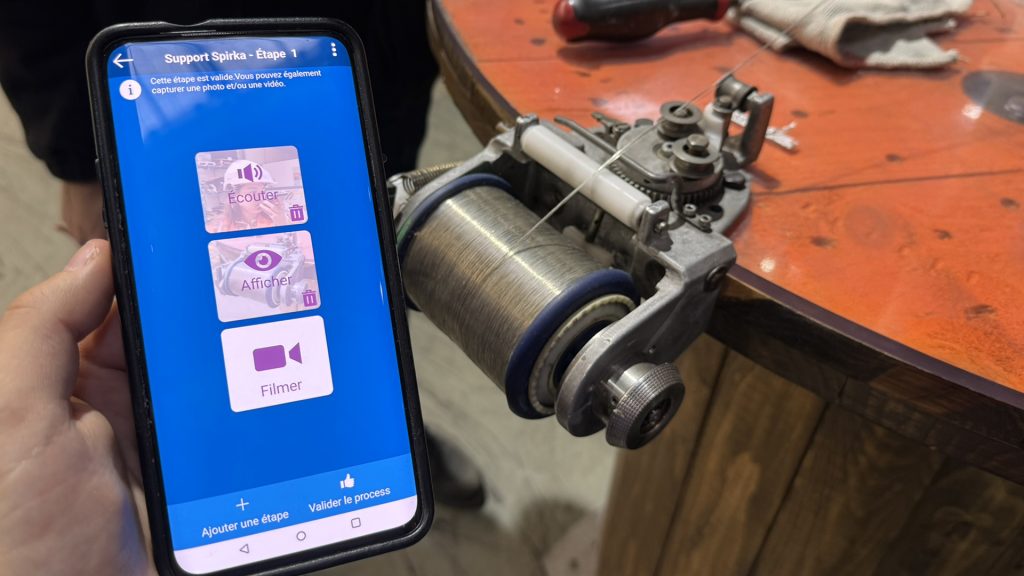
L’IA permet de créer une procédure à partir de simples commentaires. Que ce soit un document PDF existant ou les explications fournies par un expert sur le terrain, l’IA de Dimeo propose de reformuler et restructurer automatiquement ces informations de manière pédagogique et formelle. Pour créer un nouveau module, un expert méthodes peut donc aller sur le terrain enregistrer des commentaires audio, photo et vidéo sur le terrain à l’aide d’un téléphone. L’IA propose ensuite un module prêt à l’emploi à partir de ces commentaires. Le service méthodes peut également retravailler manuellement ce module à tout moment sur ordinateur.
Ces outils ont permis d’accélérer la création et la mise en place des standards. Cette comparaison s’appuie sur le temps de conception d’une fiche PDF, comparé à celui d’un module Dimeo. Jonathan Verderame nous partage son ressenti : « La prise en main est simple. C’est plus rapide de créer un module dans Dimeo que d’utiliser une trame Word ou PDF. Nous ne sommes plus obligés de réfléchir en amont à la mise en page, nous pouvons créer le module progressivement et revenir le modifier à tout moment. Un module complet et pédagogique peut-être réalisé en seulement deux jours ».
La digitalisation est réalisée de manière collaborative. Pour cela, le service méthodes inclut dès le départ les experts métiers, afin de tester les modules réalisés. Ces derniers peuvent ainsi laisser librement des commentaires et suggestions écrites ou audio pendant leur parcours. Le service méthodes prend ensuite en compte ces commentaires pour améliorer les modules en conséquence. Les tests démontrent que les experts métiers ayant utilisé au moins une fois le casque sont plus favorables à l’utiliser.
La prise en main est simple. C’est plus rapide de créer un module dans Dimeo que d’utiliser une trame Word ou PDF.
Jonathan Verderame – Superviseur des opérations des Câbleries LAPP à Forbach
La prise en main des équipes métiers en autonomie
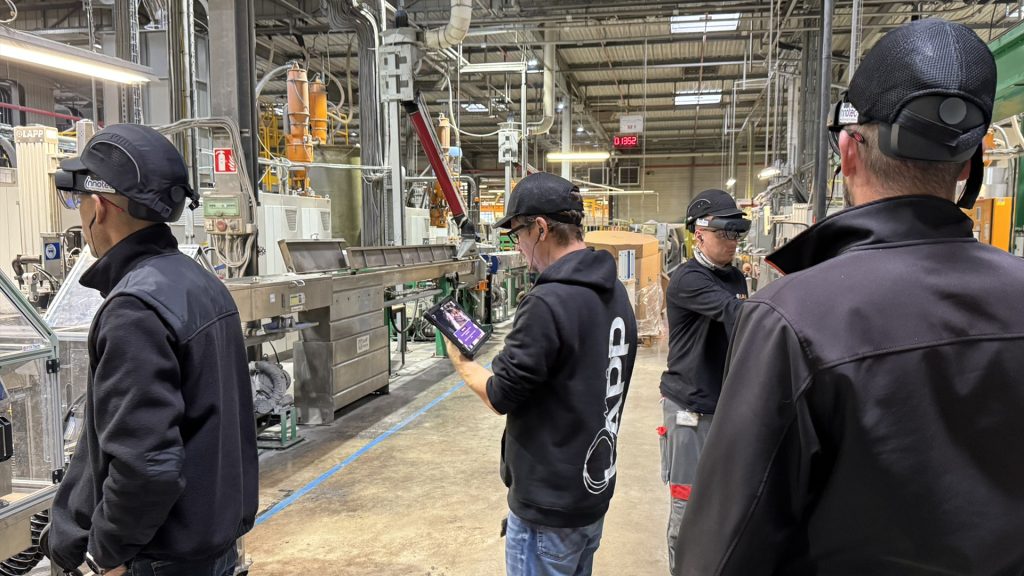
Les équipes métiers utilisent désormais l’application en autonomie. Les premiers tests ont été très positifs, favorisant un usage progressif des nouveaux arrivants et opérateurs qualifiés. Les équipes métiers apprécient l’interface épurée et agréable à utiliser, permettant d’en comprendre l’usage en seulement quelques minutes. Ils apprécient également la possibilité d’accrocher l’instruction où ils le souhaitent en Réalité Mixte. Cela permet ainsi de ne pas gêner le champ de vision lors des opérations.
La prise en main du casque se réalise en quelques minutes, grâce notamment aux commandes vocales et oculaires disponibles dans Dimeo. Il suffit de regarder un bouton ou d’énoncer à haute voix une action pour interagir avec l’application. LAPP a également réalisé des modules de démonstration. Ils permettent à chacun d’essayer le casque en salle pour se familiariser, avant de l’utiliser en opération. Le fait de pouvoir suivre la procédure tout en gardant les mains libres explique le choix de LAPP dans l’équipement du casque au profit des tablettes.
L’équipe projet confirme l’importance de faire essayer ces technologies à l’ensemble des équipes dès le départ. Ces essais ont permis de sensibiliser chaque personne à l’apport de ces nouveaux outils, augmentant leur volonté de les utiliser. Jonathan Verderame nous partage les premiers retours d’expérience : « L’accueil fut très positif. Les opérateurs entendaient leurs collègues en parler et voyaient les équipes méthodes faire les modules avec le casque au loin. Ils voulaient donc essayer par curiosité. Au final même les personnes réticentes au départ ont véritablement apprécié l’outil après leur essai, et l’utilisent désormais comme un outil de travail. »
L’accueil fut très positif, y compris auprès des personnes réticentes au départ, qui ont véritablement apprécié l’outil après leur essai et l’utilisent désormais comme un outil de travail.
Jonathan Verderame – Superviseur des opérations des Câbleries LAPP à Forbach
La suite pour Dimeo chez LAPP
Après plusieurs mois d’utilisation, les équipes estiment des gains significatifs. Cette estimation s’appuie sur les coûts liés à la formation et la mobilisation des formateurs qui en découle sur les six prochains mois. Le formateur reste partie intégrante de la formation, mais peut désormais être sollicité ponctuellement et non à plein temps, avec une grande partie de la formation réalisable en autonomie. Les apprenants sont également autonomes plus rapidement, et peuvent donc accélérer leur prise de poste. D’après les estimations des équipes de Forbach, le temps de formation s’en retrouve divisé par 2.
Un déploiement dans d’autres usines pourrait s’avérer judicieux. Les équipes allemandes ont récemment sollicité Innoteo pour obtenir une démonstration, suite à une présentation réalisée par LAPP en interne, l’objectif est de standardiser, à terme, les procédures au sein du groupe, et confirmer à grande échelle les bénéfices constatés. Les modules réalisés en France pourront être traduits automatiquement grâce à l’IA intégrée à Dimeo pour être facilement partagés.
Le site de Forbach prévoit de former 67 personnes sur un an. Julien Mazelin nous confie : « L’utilisation de nouvelles technologies comme la solution Dimeo est un levier pour attirer les talents (et les jeunes en particulier) et maintenir leur engagement dans notre industrie. ». Dimeo s’intègre désormais dans la stratégie de formation, en permettant aux techniciens d’opérer et se former plus rapidement et plus efficacement.
L’utilisation de nouvelles technologies comme la solution Dimeo est un levier pour attirer les talents (et les jeunes en particulier) et maintenir leur engagement dans notre industrie.
Julien Mazelin – Directeur Général des Câbleries LAPP à Forbach